Predictive maintenance has become a game-changer in the industrial landscape, allowing companies to move beyond reactive repairs and embrace proactive care for their equipment. But with three main types vying for attention – indirect failure prediction, anomaly detection, and remaining useful life (RUL) – it can be overwhelming to choose the right approach. Let’s delve into each method and see how Qritrim’s solutions can help you navigate the world of predictive maintenance.
Indirect Failure Prediction: Keeping an Eye on the Health Score
Imagine your equipment having a health score, constantly fluctuating based on its maintenance needs, operating conditions, and historical performance. That’s the essence of indirect failure prediction. This method relies on readily available data and existing sensors, making it a scalable and cost-effective option. Qritrim’s AI-driven analysis takes this approach to the next level, providing you with valuable insights into your equipment’s health, even without extensive failure data.
Anomaly Detection: The Sherlock Holmes of Equipment
Think of anomaly detection as a detective for your equipment, constantly looking for irregularities in its data. This method identifies deviations from normal operation patterns, potentially signaling impending problems before they cause major disruptions. The beauty of anomaly detection lies in its low data and hardware requirements, making it ideal for situations where detailed historical data is scarce. Qritrim’s AI-powered anomaly detection empowers you to act proactively on potential issues, minimizing downtime and maximizing efficiency.
Remaining Useful Life (RUL): Predicting the Future of Your Equipment
Wouldn’t it be amazing to know exactly how much life your equipment has left before needing attention? RUL does just that, providing an estimated usage time remaining before repair or replacement is required. This approach is particularly valuable for high-cost equipment where downtime can be crippling. While RUL models demand powerful computing resources and may require retraining for specific cases, Qritrim’s RUL estimation offers robust and reliable predictions, enabling you to plan maintenance with confidence.
Choosing the Right Tool for the Job
The best predictive maintenance approach for you depends on your unique needs and priorities. Consider factors like:
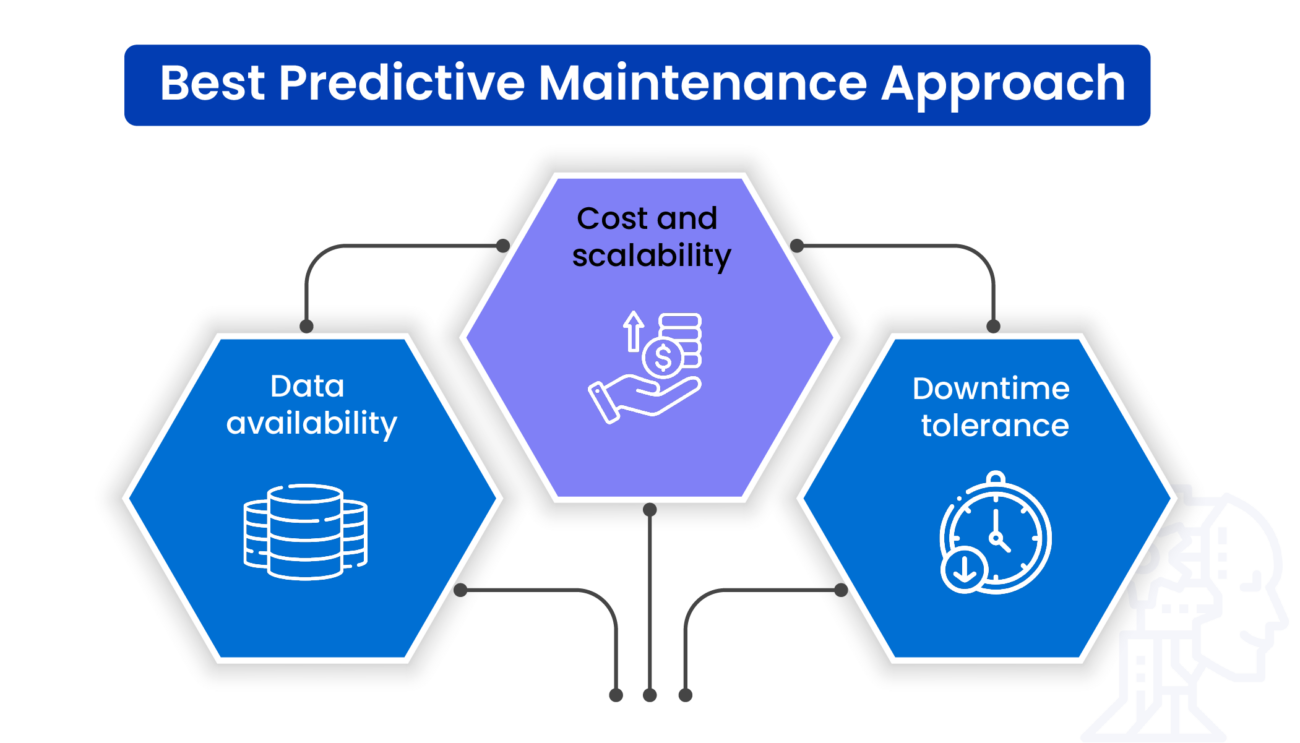
- Cost and scalability: If budget is a concern, indirect failure prediction or anomaly detection might be the way to go.
- Data availability: If historical failure data is limited, anomaly detection shines.
- Downtime tolerance: For industries where downtime is costly, RUL can be a lifesaver.
Qritrim: Your Partner in Predictive Maintenance Success
No matter which approach you choose, Qritrim is here to be your partner in predictive maintenance success. Our AI-powered solutions are designed to unlock the full potential of your data and provide you with actionable insights that can transform your operations.
Ready to take control of your equipment’s future? Contact Qritrim today and discover how we can help you optimize your maintenance strategy and achieve peak performance.